Three-Stage Pumps: the solution for critical pressurized fluids
Three-stage pumps are centrifugal pumps designed to handle high-pressure applications by utilizing three impellers arranged in series. These pumps are essential in industries that need to manage continuous and pressurized flow of fluids. Pemo Pumps experience tells that this kind of pump offers advantages in performance, energy efficiency, and fluid handling capabilities compared to single-stage pumps.
In this article, we’ll explore what Pemo three-stage pumps are, how they work, where they are commonly used, and what are their main components.
Three-Stage Pumps, the definition
A three-stage pump is a multi-stage centrifugal pump that uses three impellers to increase the pressure of a liquid being transported. Each stage consists of an impeller and a diffuser, which work together to increase the velocity and pressure of the fluid at each successive stage.
Pemo three-stage pumps are used in applications requiring moderate to high pressure and relatively constant flow rates. These pumps are engineered to operate efficiently over long periods, making them suitable for industrial and commercial uses too. And, which is more important, Pemo three-stage pumps are build to be anti acid and anti abrasive, to preserve pumps life and to be ready for the use with every type of slurry and sledge fluid.
How do three-stage pumps work exactly
The principle of a three-stage pump is based on the centrifugal force generated by the rotating impellers. When liquid enters the pump, it is directed toward the first impeller, which spins it at high speeds. This impeller adds energy to the fluid by converting mechanical energy from the motor into kinetic energy. The velocity of the liquid increases, and it is pushed outward toward the diffuser, where the kinetic energy is transformed into pressure.
The fluid enters the pump, passes through the first stage, where its pressure is increased, then moves to the second stage for further pressure increase, and finally to the third stage, which adds the final boost in pressure before the fluid exits the pump.
The key benefit of using three stages is the ability to increase pressure without significantly reducing the flow rate. This makes three-stage pumps particularly useful in applications where it is necessary maintaining a steady and pressurized flow over a long distance or at a high elevation, for example in mining sector.
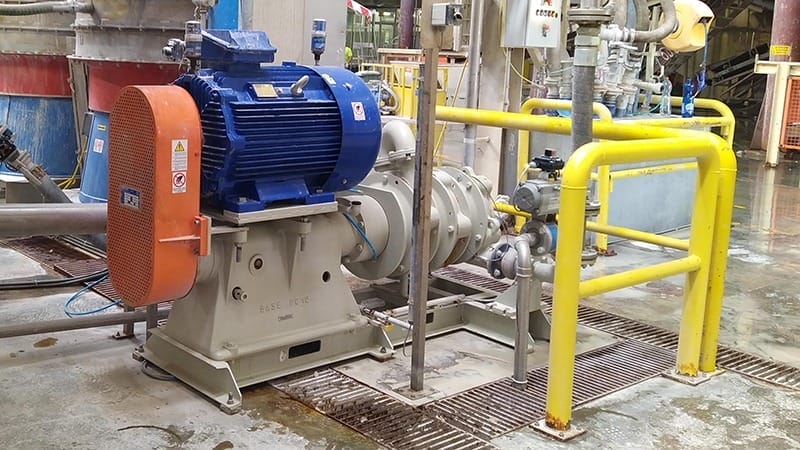
Which are the components of a three-stage pump
Now, we can see which are the main components of a three-stage pump. These include:
- Impellers.
The impeller is the most crucial component of a pump: it is responsible for adding velocity and energy to the fluid. In a three-stage pump, we have three impellers, one for each stage. Each impeller is mounted on a rotating shaft and spins to propel the fluid through the pump. - Pump Casing.
The casing encloses the impellers and diffusers, providing protective housing for the pump’s internal components. It could also help maintain the pressure of the fluid as it moves through the system. - Shaft.
The impellers are mounted on a central shaft, which is driven by an electric motor. The shaft transmits mechanical energy from the motor to the impellers, enabling them to rotate and move the fluid. - Suction and Discharge Ports.
These ports are the entry and exit point for the fluid. The suction port allows the fluid to enter the pump, while the discharge port releases the pressurized fluid after it passes through all three stages. - Seals and Bearings.
Seals prevent leaks in the pump casing, while bearings support the rotating shaft and reduce friction, ensuring smooth operation. Proper lubrication of these components is essential for long-lasting pump performance.
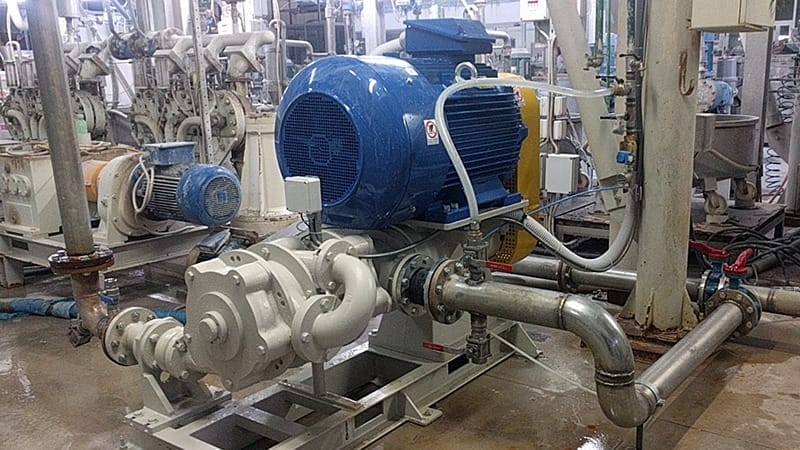
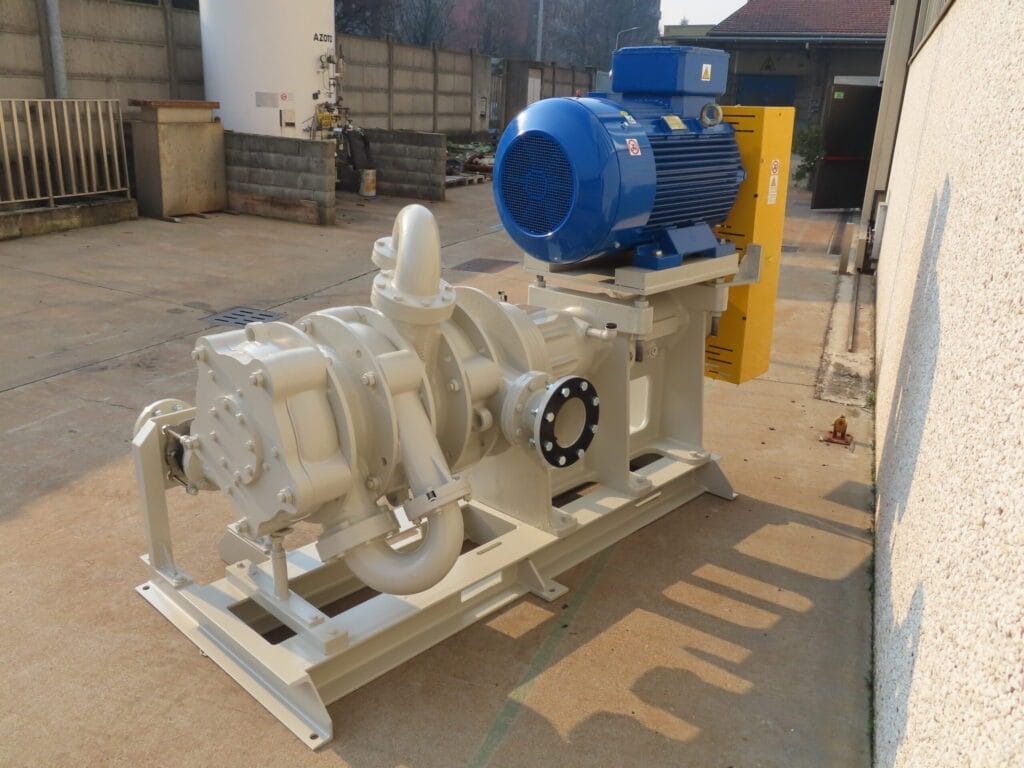
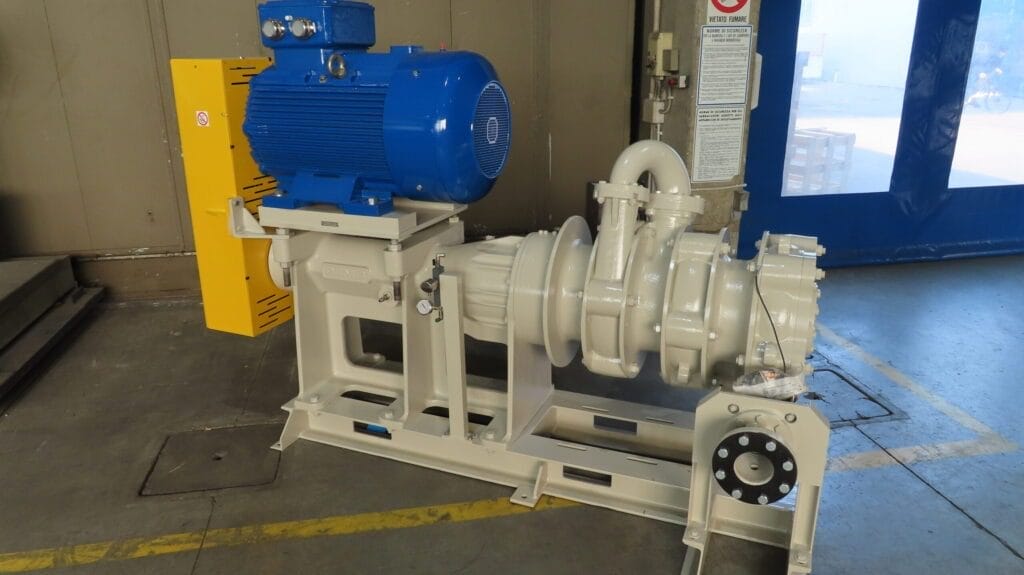
Industrial applications of three-stage pumps
Three-stage pumps can be found in many industries that require the movement of liquids under pressure. Some of the common applications where the three-stage Pemo pumps are used, include:
- Ceramic.
In the ceramic sector, three-stage pumps are usually used to transfer of slips or glazes. They also pumps muddy waters coming from all working areas for their elimination or for the recovery. They pump thickened sludge and are used for the dehydratation of the ceramic muds. - Oil and Gas industry.
In the oil and gas sector, three-stage pumps are used for pipeline transport, water injections in oil wells, and pumping crude oil. These pumps are crucial in maintaining the flow of fluids through extensive pipeline systems and in offshore drilling operations, where high-pressure water injections are often required to enhance oil recovery. - Mining and Construction.
In the mining industry, three-stage pumps are employed to pump water, slurries, and other liquids in and out of mining operations. They are also used in construction projects for dewatering flooded areas, excavations, and tunnels. - Filter press systems.
Three-stage pumps are specifically designed to handle the unique requirements of filter press systems, which are widely used in various industries for solid-liquid separation.
Main advantages of three-stage pumps
Three-stage pumps offer several advantages over single-stage or two-stages pumps, let’s see what they are.
Three-stage pumps can generate higher pressure than single-stage pumps. Since three-stage pumps are designed to operate at optimal efficiency, they can provide the desired pressure and flow without consuming excessive energy. Compared to using multiple pumps in series, a single three-stage pump offers a more compact and space-saving solution. Finally, three-stage pumps are built to handle demanding environments and are often more durable than single-stage pumps due to their reinforced design.
Is there any challenge in using three-stage pumps?
The use of three-stage pumps has also some challenges to consider, let’s see what they are:
Due to their complexity and the number of components, three-stage pumps require regular maintenance to ensure efficient operation. Bearings, seals, and impellers must be inspected periodically to avoid wear and tears, which can lead to reduced performance or pump failure.
If multi-stage pumps tend to be more expensive compared to single-stage pumps, their long-term energy savings and superior performance often offset the higher initial cost.
Like other centrifugal pumps, three-stage pumps are susceptible to cavitation, which occurs when the pressure in the pump drops below the vapor pressure of the liquid being pumped. This can cause vapor bubbles to form and collapse, potentially damaging the impellers and reducing pump efficiency. You can solve this issue with periodical maintenance.
At the end of the day, three-stage pumps are essential tools in various industries requiring high-pressure fluid handling. Their ability to maintain consistent pressure and flow over long distances or in complex systems makes them invaluable in oil and gas, water distribution, firefighting, power generation, and more. The efficiency, reliability, and versatility of three-stage pumps continue to make them a preferred choice in demanding industrial environments.
Pemo Pumps is an Italian excellence in the custom pumps market. With a production 100% made in Italy, 60% of Pemo Pumps revenues comes from direct sales worldwide. Just one third of our sales are to Italian companies for direct use and for selling wordwide. Pemo Pumps has subsidiaries, representatives, and agents in 20 Countries and has more than 4,000 customers in the World.>
Contact today our consultants to learn more about the complete range of Pemo Pumps.