What are two-stage pumps
Two-stage pumps, also known as two-stage hydraulic pumps, are a type of pump that utilizes two gear pumps to optimize performance without the need for increased horsepower. These pumps are designed to combine flow at low pressures using both gear pumps and switch to a single pump at high pressures. This dual functionality allows for high flow rates at low pressures or conversely, high pressures at low flow rates, making them highly efficient for various applications.
The mechanism behind these pumps involves the movement of oil or another fluid by the gears, with the pressure being a byproduct of resistance to the fluid’s flow outside the pump. They are commonly used in equipment like log splitters, where they can significantly improve speed and efficiency.
The design of two-stage pumps is such that they provide a fixed amount of fluid displacement with each rotation, which is a characteristic of positive displacement pumps. This ensures a consistent flow rate that is determined by the pump’s displacement and the rotation speed.
Two-stage pumps are valued for their simplicity, cost-effectiveness, and ability to handle dirty oil, which makes them prevalent in the market. In essence, these pumps are an innovative solution for achieving desired pressure and flow dynamics in hydraulic systems without necessitating larger engines or increased power consumption.
Pemo two-stage pumps
Let’s now take a look to the Pemo two-stage pumps. Pemo has a little o no competition with their two-stage and three-stage pumps in filter-press feeding.
Capacities of our two-stage pumps when filling the filter press can reach 2000 m3/h (9000 GPM). Also final Pressure can exceed 20 bar (290 psi) for the Triple Stage and for some Two Stage Models, creating a much dryer cake than single stage pumps can provide. We have more than 40 models available and 12 models of PEMO two-stage pumps are built with power from 30 to 250 kW (40 – 340 HP) and flows from 30 to 600 m3/h (130 to 2600 GPM).
The AO/AB/DC Pemo Pumps versions have multiple stages connected in series that can be made with rubberised casings and Hardalloy impellers or in all-Hardalloy versions. These ones are built in order to reach 24 bar (350 psi) with ceramic slip or metal concentrates. The flow rate remains constant while the head increase.
Pemo two-stage pumps become the perfect solution for the feeding of filter presses, or they transfer slurries when the geodetical distances or the pressure loss due to the piping are very high.
AO/AB/DC SERIES (two-stage versions)
- Designed for slurries and/or acid applications.
- The AO/AB/DC Series is the perfect solution for filter press feed or slurry transfer.
- When pumping acid liquids, the shaft and the mechanical seal housing can be made of special alloys.
- Maximum particle size is 1 mm, though this is dependent on the specific application.
- Capacities from 5 a 900 m3/h (22 to 2,645 gpm).
- The maximum head for some Hardalloy versions is 210 m/H2O.
These are AO/AB slurry pumps but with two bodies installed on the same shaft so that, working in series, high pressures (up to 12/15 atm) can be obtained, particularly suitable for feeding filters for high pressing.
Advantages of two-stage pumps
Two-stage pumps offer a significant advantage over single-stage pumps in terms of efficiency and performance. While single-stage pumps operate at full capacity all the time, two-stage pumps can run at a lower capacity when full power isn’t needed. This means that two-stage pumps can adjust their output to match the demand, which can lead to energy savings and reduced wear on the pump components.
In applications where varying flow rates are beneficial, such as in climate control systems or industrial processes, the versatility of two-stage pumps makes them a superior choice. Additionally, the two-stage operation allows for better control of the fluid flow, which can be crucial in applications requiring precise pressure adjustments.
On the other hand, single-stage pumps are typically less complex and may be more cost-effective for applications where a constant flow rate is sufficient. They are also generally easier to maintain due to their simpler design. However, the lack of flexibility in operation means that they may not be as efficient in systems where the demand for flow or pressure fluctuates. Ultimately, the choice between two-stage and single-stage pumps will depend on the specific requirements of the application, including the need for efficiency, control, and cost.
Two-stage pumps applications
Two-stage pumps are versatile and efficient, making them ideal for a wide range of applications where precise control and variable flow rates are required. They are particularly effective in scenarios where the demand for pressure and flow varies, allowing for a more energy-efficient operation. Some common applications where clients use Pemo two-stage pumps are:
- Vacuum Furnaces and Metallurgy. In metallurgical processes and vacuum furnaces, two-stage pumps help produce high-quality, pure metals by maintaining controlled environments free of impurities and oxygen.
- Food Packaging and Processing. The food industry benefits from the use of these pumps in packaging and processing, where maintaining a specific atmosphere is crucial for preserving the quality and safety of food products.
- Pharmaceuticals and Chemicals. Two-stage pumps contribute to the creation of clean and stable conditions necessary for production and research.
- Mine Dewatering. They are employed in mining operations to manage water levels in mines, ensuring safety and efficiency.
- In Agriculture, these pumps are used to provide water at the right pressure for irrigation systems.
- Oil and Gas Production. In the oil and gas industry, two-stage pumps are used for various tasks, including fuel delivery and operational processes.
- Power Plants. Boiler feeder pumps in power plants utilize these pumps to handle the high-pressure requirements.
These examples highlight the adaptability and efficiency of two-stage pumps across various industries, demonstrating their importance in modern technology and industrial processes. Their ability to provide high pressures and flow rates while maintaining energy efficiency makes them an invaluable component in many applications.
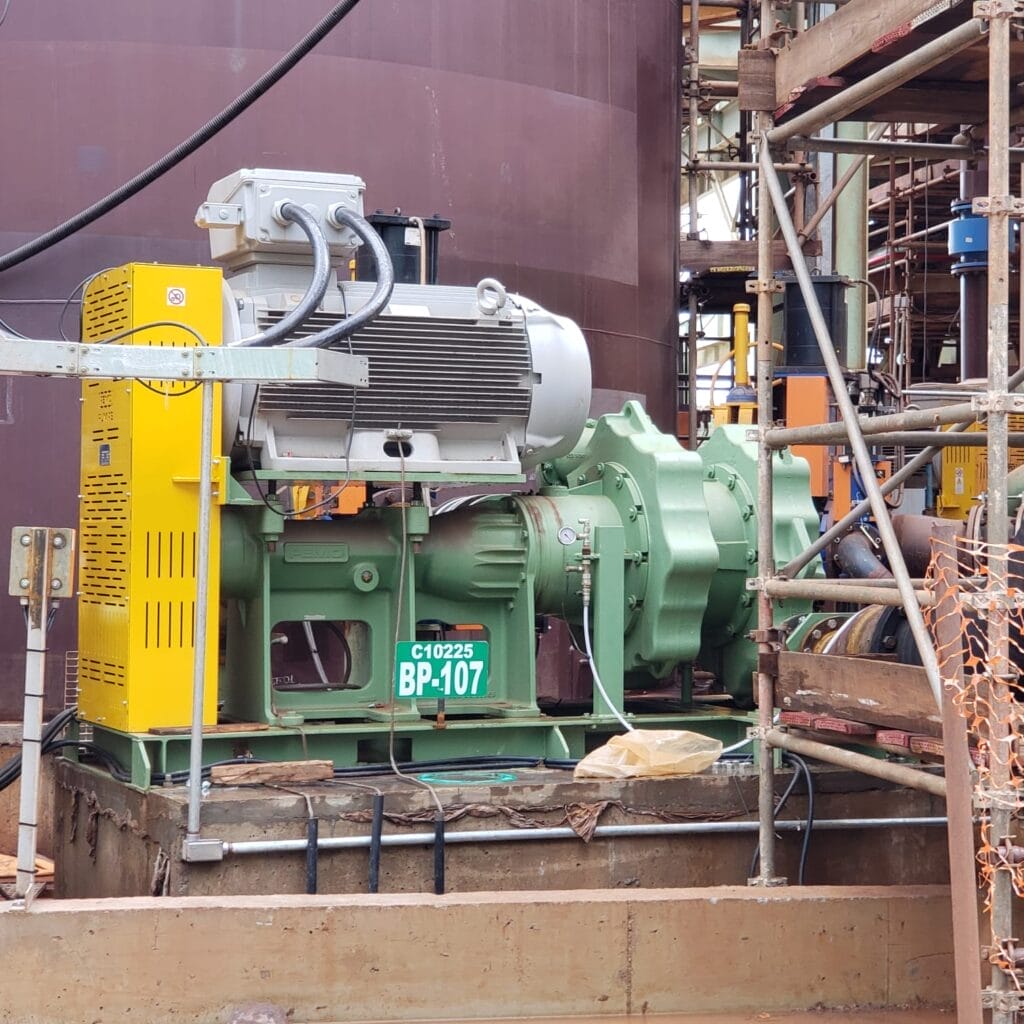
SUITABLE FOR:
- Applications under head
- Abrasive liquids
- Acid liquids even with solids in suspension
- Operating temperature up to 90 °C
TYPES OF SEALING:
Mechanical seal with front rings double flushed or with permanent lubrication.
MINIMUM MAINTENANCE
Pump/motor coupling:
- By means of pulleys and V-belts
- By means of elastic coaxial joint
Pemo Pumps is an Italian excellence in the custom pumps market. With a production 100% made in Italy, 60% of Pemo Pumps revenues comes from direct sales worldwide. Just one third of our sales are to Italian companies for direct use and for selling wordwide. Pemo Pumps has subsidiaries, representatives, and agents in 20 Countries and has more than 4,000 customers in the World.
Contact today our consultants to learn more about the complete range of Pemo Pumps.